PID tuning normally requires the DCS engineer to have a good knowledge of the process and the control strategy, and specially time. While other also important activities are waiting the conventional bump-test-tuning procedure gets more complicated when tuning master-cascade strategy loops, when two, or often more, variables need to be tested and each of the loops individually tuned. To make the challenge even greater, these loops are normally configured for important and slow response variables, such as temperatures in distillation columns, or reactors.
In these cases, what would be only a simple PID parameter modification, turns out to take days after having affected the product quality and/or the throughput.
The best way out in this scenario is to do it right and at the first try. How? That is what I’ll explain in this blog.
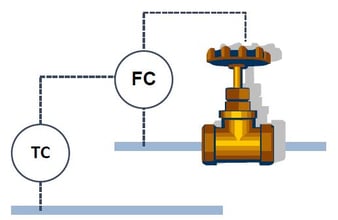
Getting it done - PID tuning
To set the right tuning for a master-slave pair, the tuning recipe is applied twice in sequence. As the secondary controller is part of the “process” from the primary loop point of view, any alteration to it, by means of new tuning, algorithm or filter, for example, impacts directly on the master controller. With this in mind, we always start from the slave loop, and a common workflow is as follows:
- Put the loop in MANUAL mode and perform some bump tests in the controller OP. It is important to have the process stable during the tests and to use steps that are big enough so a good response can be obtained. Better if the whole normal operation region is covered by the tests.
- Identify the process model (gain, time constant and dead time) and use the correct tuning rules, given the process dynamics, to calculate the new set of parameters. It is noteworthy considering the more robust scenario, that means the region where model has the higher gain, and choosing the correct rule for the given process dynamic.
- Put the loop in AUTO and change the PID parameters to the new set. It is important to move gradually in the direction of the revised parameters, so to avoid abrupt changes in the response.
- Perform some additional testing to check the loop performance.
Once the slave response is good enough it is time for the master loop tuning:
- Keep the master loop in MANUAL mode and perform some bump tests in the slave loop SP. This is equivalent to set the inner loop in CASC mode and performing the bumps in the master control OP. Take same precautions as before
- Identify the process model (gain, time constant and dead time) and chose the proper set from the known tuning rules or with trial and error methods. Here the choosing of the tuning rule, or the trial and error, should be done carefully as a master should not be more aggressive than the slave.
- Put the master loop in AUTO while setting the inner loop with CASC mode. Change the set of parameters gradually.
- Perform some testing to check the combined loop performance.
For a master-slave pair, the relative velocities are also important:
- Adjust the parameters so the responses are correctly paced. The master controller cannot be too aggressive but should allow the inner loop to do its job and that is not straightforward even when the tuning rules are applied.
The same precautions as for the tuning of single control loops are to be considered for a cascade strategy. That means taking into account process characteristics, such as expected disturbances, the loop objectives, as setpoint tracking or load rejection, the DCS features, and so forth.
Even though this procedure can result in a satisfactory set of parameters, it can be time consuming and not necessarily effective. Following these steps for each of the cascade loops in the process and you might have gone through multiple tuning iterations, spent a lot of time and, still have some poor performances. This would be remarkably wasteful and expensive.
Getting the optimal set of PID parameters
PID tuning tools can reduce the complexity of this task while delivering better performances. Before the software can make this calculation, it needs to know how the process responds and how fast or how slow it gets there. You still need the process to be tested, but only the first trial for the inner cascade loop and that means the roughly 9 steps procedure would be well simplified.
Instead of a “decent” tuning, the PID tuning software helps you to achieve the optimal set of parameters for the two loops simultaneously. You will have a slave loop that is fast but still robust, and a master controller that meet your performance design criteria, like for example its rise time or the gain margin. As important as the best loop performance, the time consumption, and hence the costs, are drastically reduced.
PID tuning software does it right at the first try
It takes time to run tests and tune complex PID loops. The PID tuning software get it right and at the first try. No need to manually iterate the PID parameters, no need to adapt them to the DCS equation, no need to test the master loop again, no need to check relative velocities. No waste of time. Choose a PID tuning software for cascade loops — you get:
- Fewer interventions during the tuning
- Loops that meet the given performance criteria (rise time, gain margin or overshoot, for example)
- More robust tuning
- Better control of the key variables of the process
Read more about using AptiTune on cascading loops on a NGL recovery plant in the case study below:
Do you like to know what INCATools PID tuning software can offer you?
Request your demo here.