A split range control strategy uses software or hardware-based splitter and two or more final control elements to control a process variable. Split range strategies can be found in different applications across process industries: temperature control with heating/cooling media, large and small valves installed in parallel, pressure control with a vent valve, etc.
Usually, split range applications are tricky and time-consuming, and you should know what I’m talking about as a process control engineer
Oscillations over the entire range of operation and across the split point, typically improperly selected at 50%, are common in real operation.
In this blog, we will discuss the usual problems you might face when configuring and tuning a split range strategy and the possible and practical solutions to overcome it.
Split range control challenges
Clients often call us to check the performance of their split range strategies. Split range applications are challenging, so don’t feel bad and lonely if you face this in your plant. It is more common than you think!
Your split range strategy could be causing oscillations and process instability due to different factors:
- Sub-optimal PID tuning
- Wrong selection of the split point
- Poor control valve performance (control valve stiction, deadband, type, etc.)
- Non-linear installed control valve characteristic
- Poor actuator/positioner performance
- Process non-linearities (process dynamics differs over the range of operation, e.g. cooling/heating, gas/liquid)
There is good news: you can apply a comprehensive approach and consider the split range strategy as a whole and not die trying.
How to succeed and not die trying?
These tips will help you, read them carefully:
- Use the right tools to identify the process dynamics for the entire range of operations and compute optimal PID tuning parameters. If it is required, you should implement PID tuning scheduling based on the PID controller output (PID tuning parameters can be changed automatically based on the PID controller output). INCATools can help you out to achieve this.
- Select the split point based on the control valves and process gain. The most common practice is to select the split point as 50%. However, this only applies if the control valves sizes and operating conditions are the same for both control valves. If the process gain is unknown (i.e. in new applications), you can use the control valves flow coefficient (Cv/Kv) to develop an initial split point.
- Use a control valve designed for throttling with a smart positioner, the right actuator, excellent resolution and response time. Control valves often suffer from mechanical problems (e.g. stiction, deadband) near the closed position. The use of overlap in the split configuration can be useful (see image below).
- Do not configure a deadband in the split range strategy. A deadband might only increase the oscillations around the split point.
- Use a “software-based” signal splitter. This will make your life and job easier. The advantages are:
- Easy to maintain
- Easy to understand
- Flexibility to implement split range strategy variations (split point and overlapping configuration)
- Centralization of the split range logic in the control system
- Reduction of physical failure points
- Last but not least, you must provide proper training and information to the operators.
What benefits could you get from a well configured and tuned split range strategy?
Typical benefits include:
- Savings on control valve maintenance as wear and tear is reduced.
- Energy savings (e.g. steam, cooling water, gas, compressed air, etc.)
- Reduced process variability
As a practical example, you can think of a batch reactor operation: it can waste energy from oscillations in the reactor temperature, especially around the split range point. Is not this a powerful reason to pay more attention and improve your split range strategies?
So, if you want to learn more about how to go from the behaviour of the first table to the last:
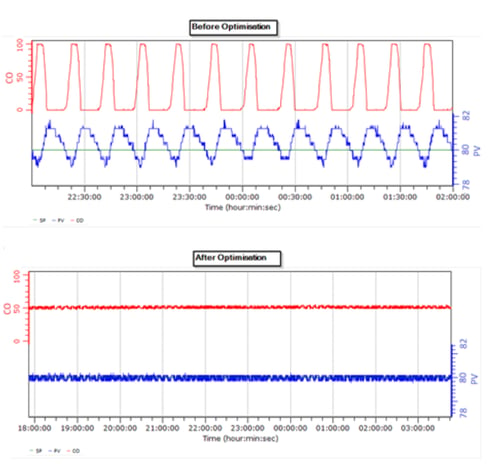
We are happy to advise you about how PID tuning, process knowledge, and the right tools can help you accomplish optimized plant performance. Plan a meeting with one of our Control experts here.