Batch reactors are used to produce a variety of products in all sectors of process industries, especially in the pharmaceutical, specialty chemicals, wastewater treatment and the beverage sector. The flexibility to use the same equipment to produce different products sometimes makes batch reactor difficult to control. If we add to this the integrating/runaway process response, suboptimal PID control loop tuning, poor control loop elements performance, and an inappropriate process and control design, we might have the perfect recipe for disaster. If you want to learn more about obtaining optimal batch reactor temperature control, keep reading the blog.
Batch reactor process
A typical batch process cycle can be mainly described as:
- Chemicals and reactants are loaded in the reactor and heated to a desired temperature.
- Temperature is kept at the desired value. Fast response with no oscillations and minimum overshoot is essential when setpoint changes are performed and a stable response when disturbances are present.
- Final product is pumped to storage.
Chemical reactions might be exothermic/endothermic so cooling/heating might be required to maintain the reactor temperature at the desired value. Typically, a reactor temperature control is implemented by using a split range strategy that adjusts cooling/heating media, but this is not the only option. You can find different temperature control strategies depending on the process objectives, process constraints, reactor type, etc.
Reactor temperature control affects reactor performance which in turn affects product quality, raw material and energy consumption, yield and operating costs.
Batch Reactor Temperature Control Challenges
In practice, it’s not uncommon to have a batch reactor temperature control oscillating around the setpoint. In addition to this, it’s also common to have an overshoot when the temperature controller setpoint is changed; this is due to the integral action both in the PID controller and in the process dynamics (integrating/runaway process response). However, alternatives are available to reduce or prevent this behaviour, such as tuning rules, different PID control structures/algorithms, and strategies.
Follow these steps, and you will end up having the perfect recipe for improving your batch reactor temperature control:
- Identify the process dynamics: Run some step tests with the PID loop in manual mode (if possible) and use a software tool to identify the process model for different operating ranges and different products. INCA Tools can help you with this!
- Assess the need to implement PID scheduling or adaptive tuning: Once the process model is obtained for different operating ranges (cooling/heating) and products,, check how process dynamics differ. If the process dynamics are quite different, then PID scheduling/adaptive tuning is suggested. With PID scheduling/adaptive tuning one set of tuning parameters is automatically loaded into the PID block depending on the operating range and batch.
- Choose the right temperature control strategy: Depending on the type of reactor, heating/cooling system, and control objectives, the strategy can differ, e.g. a cascade control strategy with the reactor temperature controller acting as the master controller and the jacket/coil temperature controller acting as the slave controller.
- Check the PID control loop elements performance:
- Reduce the control loop deadtime as much as possible.
- Select and size the control valves properly.
- Reduce control valves deadband/stiction.
- If you are using a split range strategy to control the batch reactor temperature, then assess the option to implement an overlap in the split configuration: Often, control valves suffer from mechanical problems (e.g. stiction, deadband) near to the closed position, which causes oscillations around the split point. If this is your case, then adding an overlap to the split range configuration can be useful.
- If you are using a split range strategy to control the batch reactor temperature, choose the split point appropriately: Select the split point based on the control valves and process gain. The most common practice is to select the split point as 50%. However, this only applies if the control valves sizes and operating conditions are the same for both control valves. If the process gain is unknown (i.e. in new applications), then you can use the control valves flow coefficient (Cv/Kv) to come up with an initial split point.
- Choose the right PID control structure and algorithm: You can get some benefits from selecting a PI or PID structure. Obviously it will depend on the process objectives.
- Choose the right tuning method: A tuning method that gives a non-oscillatory response would be the best choice. Some tuning methods available in the literature are designed to have oscillations in the response!
- Choose the right tuning parameters: For batch reactor temperature control, there is a tendency to use a small controller gain and small integral time (too much integral action). Generally, the optimal PID parameters should be a high controller gain and high integral time (low integral action). INCA Tools can help you find the optimal PID tuning parameters for your batch reactor temperature controller!
What benefits could you get from a well configured and tuned split range strategy? (results)
After applying the recipe for success, the typical benefits you can get are:
- Maximize product quality.
- Maximize yield.
- Minimize cycle time.
- Reduce process variability.
- Energy savings (e.g. steam, cooling water, gas, compressed air, etc.)
Figures below show the performance of a batch reactor temperature control before and after applying the recipe for success:
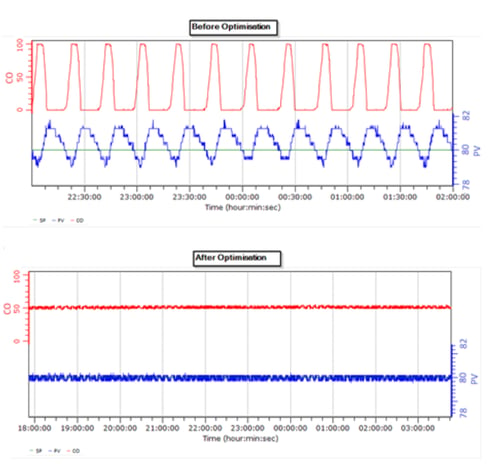
For this case (exothermic reactor), both the controller gain and integral time was increased (integral action was reduced).
The controller gain was changed from 50 to 150 and the integral time from 0.5 min to 13 min.you might have a very high unusual controller gain, so do not be afraid of it!
We are happy to advise you about how PID tuning, process knowledge and the right tools can help you accomplish optimized plant performance. Talk to an expert here.